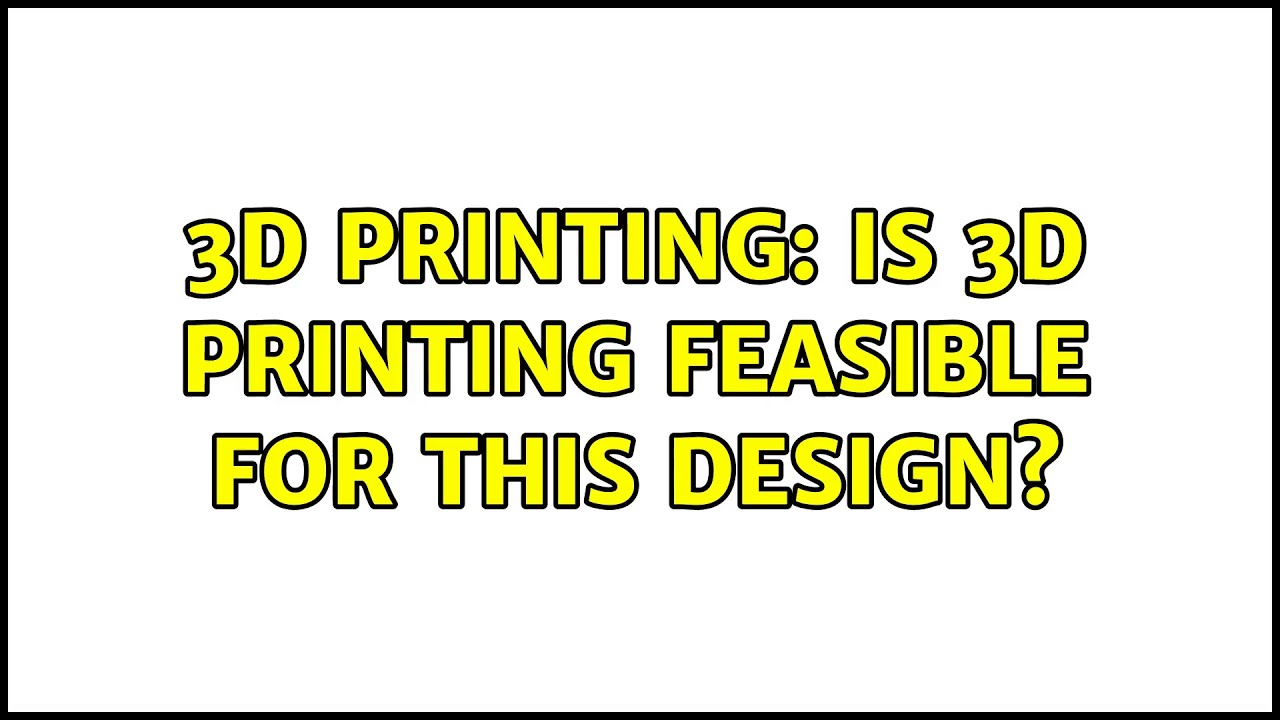
The Question: In a design that I need to prototype, I have a coaxial, rotational joint
between 2 cylinders connected to another coaxial rotational joint between 2
cylinders by a hinge. I have attached the individual part files as well as
their assembly where you can use your mouse cursor to check how they move.
Initially when I 3d printed them by splitting them in half, the outer tube did
not close, even after filing the inner tube sufficiently.
Could you tell me an alternative method to get this complicated joint working?
I need to 3D print them. I plan to use ABS for the 3D printing.
Thanks for your patience :)
EDIT: Lubrication: I plan to use grease to lubricate the sliding surfaces.
Clearances: I printed them without clearances initially (this is my first ever
3D print and I wanted to know how accurate it would be). I then used Dremel and
filing tools to file away about 0.5 mm of both the surfaces. It should have
been enough for mating the parts. The gap between the edges of the outer shell
while trying to close it around is 3-4 mm which doesn't suggest 3D printing
inaccuracy. I suspect that the outer tube isn't circular enough in cross
section. It meets the inner tube at the the two ends of the semicircle and not
inside its belly (you can see it in the picture). I have already tried the
obvious, which is removing material from the surfaces wherever the parts touch.
The model seems to be too warped for any success. The parts were printed
upwards from the bottom, so it is not the warping due to gravity.
Solutions: Please watch the whole video to see all solutions, in order of how many people found them helpful
== This solution helped 3 people ==
Have you considered to use a service to have the part printed? You can print
almost anything in one "pass" using selective laser sintering, typically done
in nylon. I am currently un-boxing an SLS printer, so I cannot currently offer
to print it, but the capabilities of SLS are substantial for parts of this
nature. I've read of entire planetary gearboxes being printed, fully assembled,
with appropriate clearances for operation, once removed and "dusted," or
cleaned of residual powder.
The printer I hope to be assembling soon has 80 micron powder, so the
resolution is quite high, although I forget at the moment the x/y/z figures.
Do you think such a method would suit your purposes?
Edit (add):
because FDM printing by nature causes "oozing" especially in the x/
y directions, I would not be surprised to learn that your outer piece has a
smaller inside diameter than your design has specified. You may have to make
adjustments to the design to compensate. Those adjustments would be specific to
a particular printer/filament combination as well. Calibration prints would
make the task slightly easier.
== This solution helped 1 person ==
Depending on your tolerances and how many you need - and how valuable your time
is - you can 3D print in ABS with a regular FDM printer, then clear out support
material and do an Acetone vapor treatment or vapor wash. It will be smooth
enough for most prototypes.
With thanks & praise to God, and with thanks to the many people who have made this project possible! | Content (except music & images) licensed under cc by-sa 3.0 | Music: | Images: & others | With thanks to user Tormod Haugene ( user SRDC ( user Shivanand ( user fred_dot_u ( and the Stack Exchange Network ( Trademarks are property of their respective owners. Disclaimer: All information is provided "AS IS" without warranty of any kind. You are responsible for your own actions. Please contact me if anything is amiss at Roel D.OT VandePaar A.T gmail.com.
0 Comments