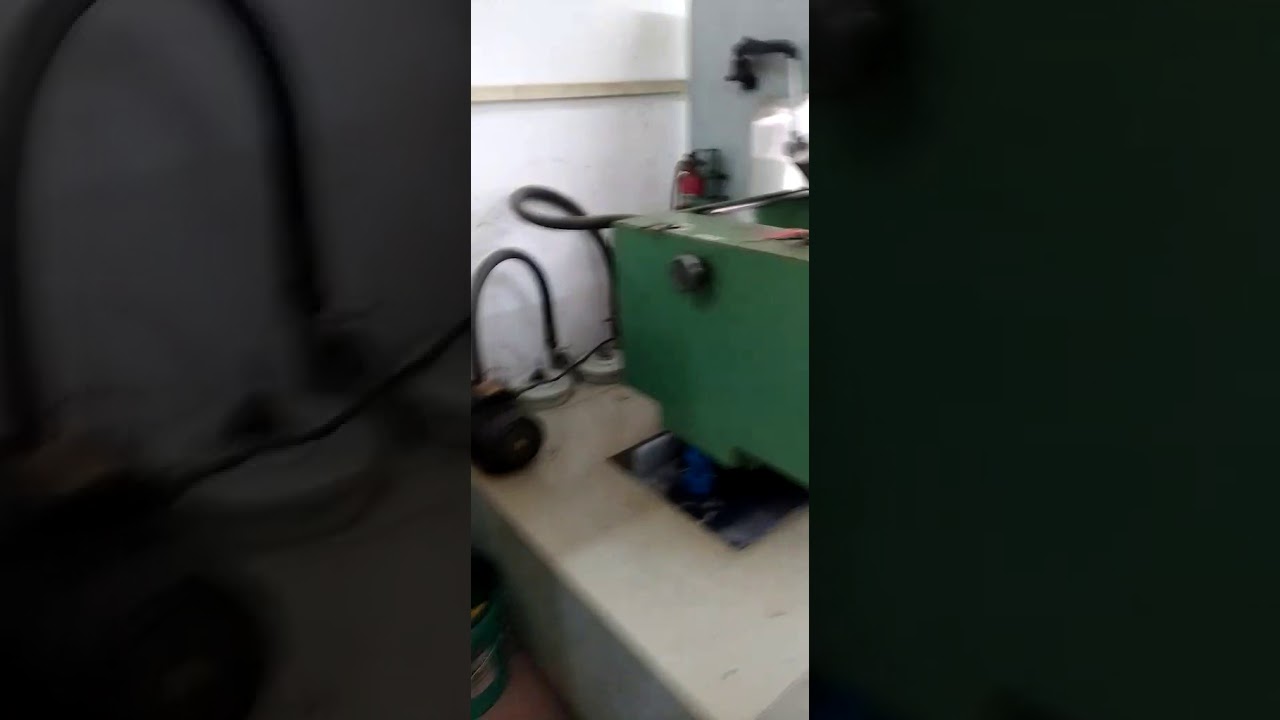
In plastic mold processing, the prerequisites for spark discharge forming are:
1. It is necessary to maintain a certain discharge gap between the electrode and the machined surface of the workpiece.(plastic mold)
This gap depends on the processing conditions, and is passed from one wire to several tens of wires. If the gap is too large, the interelectrode voltage cannot penetrate the interpolar medium, and thus no spark is generated. If the gap is too small, it is easy to form a short-circuit contact, and the spark discharge cannot be generated. For this reason, during the EDM process, It must have an automatic feed and adjustment device for electrosurgery.
2. The spark discharge must be a transient pulse discharge.plastic mold
After the discharge continues for a period of time, it needs to be stopped for a period of time, so that the heat generated by the discharge can not be conducted to the remaining part, and each discharge is limited to a small range. Otherwise, like a continuous arc discharge, the surface is burned and the size cannot be processed. For this reason, a pulse power source must be used for the electric discharge machining.
3. Spark discharge must be carried out in a liquid medium with a certain insulating property.
With the above three conditions, the digitally controlled EDM forming and processing system can perform EDM machining, and the workpiece and the electrode are respectively connected to the two output ends of the pulse power supply. The spindle head always maintains a small discharge gap between the electrode and the workpiece. When the pulse voltage is applied between the two poles, the medium breaks through the medium at a minimum relative to a certain gap or the lowest dielectric strength, and a spark discharge is generated in the portion. The transient high temperature causes both the electrode and the surface of the workpiece to etch away a small portion of the metal, each forming a small pit. After the end of the pulse discharge, after a certain interval of time, the working fluid is restored to insulation, and the second pulse voltage is applied to the electrode, and the discharge is discharged at the time when the distance between the electrodes is relatively closest or the insulation strength is the weakest, and the electric corrosion is performed. Make a small pit. Thus, with a relatively high frequency, the discharge is continuously repeated, and the electrode is continuously fed to the workpiece, and the shape of the electrode can be reproduced on the workpiece. If the electrode is convex, the shape of the workpiece is a concave shape. If the electrode is in the shape of a telephone casing, a concave and convex surface like the shape of the telephone casing is printed on the workpiece. The surface of the EDM is composed of numerous small pits.(plastic mold)
0 Comments